Let ROMAG’s mechanical engineers do the work for your custom requirements.
Our experience, engineering resources and manufacturing capabilities are
extensive.
Whether a customized version of a standard system is needed or a totally new
concept applies, ROMAG can get the job done.
Logos
We can add logos to most of our products.
Customization Options by Product Type
We can make the following modifications to existing in-stock products, which are
available more quickly and at less expense than
full
custom product development (see below).
Standard Magnetic
Snap Systems
|
Any of our standard style Magnetic Snaps
can be customized with respect to size, strength,
attachment method, or
finish. Almost all of these products
are interchangeable both as to female and male strength, dimension (i.e., 14mm
female and 10mm male) and method of attachment to
the material (for example, the male can have
a stem and the female a rivet).
|
This unusual degree of flexibility opens up a wide spectrum of applications.
Hidden Magnets
Sew-on Magnets
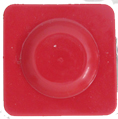 |
A large variety of plastic
housing sizes, shapes and colors can be supplied for our Sew-on Magnets.
|
Plain Neodymium Magnets
Custom Product Development
ROMAG
prides itself on designing
custom, novel closures which include magnets. The
magic of a magnetic closure enhances any product.
Rapid Prototyping – Concept to Production in 4 Weeks
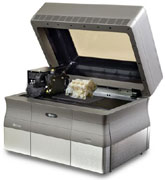
Objet 24 3D Printer |
After verifying
your requirements, we use SolidWorks CAD software to generate and present 3D
photo-real images in a digital file for your review.
Upon receiving your approval, we use the digital file to create a
plastic 3D model of the part onsite within hours, which – except for
moving parts – is an accurate representation of the final item.
Finally, if required, we can use a 5-axis
CNC milling machine to create an exact metal version of the final part. The
production parts will match this exactly since we use the digital design file
for all steps in the prototyping process as well as actual production.
|